Jeżeli już wiadomo, że materiały ogniotrwałe to nie tylko prostka szamotowa i glina, rodzi się pytanie: – do czego reszta?
Mnogość powodowana jest ekonomią – między innymi poszukiwaniem tańszego wyrobu, mogącego zastąpić droższy w miejscach o niższych wymaganiach oraz praktycznie brakiem możliwości wykonania wyrobu uniwersalnego, pozbawionego jakichkolwiek wad. Jeżeli nawet taki by istniał, pewnie i tak byłby za drogi dla realnego użytkownika.
Można zacząć od kilku słów nt. czytania kart własności (w katalogach) i znaczenia poszczególnych umieszczonych tam własności fizykochemicznych.
Poniżej przykład karty katalogowej z własnościami wyrobów szamotowych
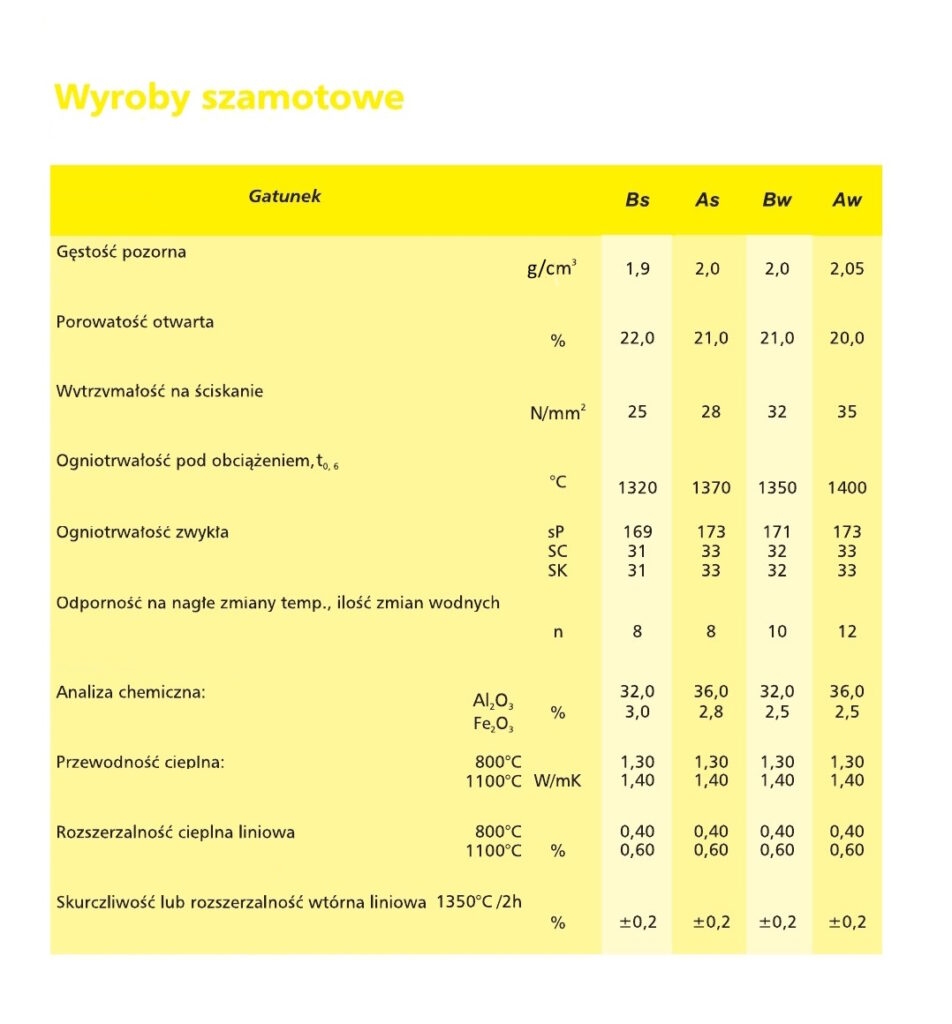
Własności materiałów.
Ogniotrwałość.
Najczęściej podawane są dwie własności o podobnej nazwie. Ogniotrwałość zwykła najczęściej nie ma dla przeciętnego użytkownika większego znaczenia. Określa ona temperaturę swobodnego mięknięcia tworzywa wyrobu. Określana jest numerem wzorcowego tzw. stożka pirometrycznego, który zachowuje się porównywalnie. Numer po pomnożeniu przez 10 daje temperaturę w oC. materiał lepszej jakości będzie zawsze miał wyższą OZ. Taki dziwny sposób pomiaru wynika z tego, że materiały wielofazowe, będące rodzajem konglomeratu różnych związków chemicznych, roztworów stałych, substancji krystalicznych i szkliw, itd., nie mają określonej temperatury topnienia, a w pewnym zakresie temperatur współistnieją w nich ze sobą stan stały i ciekły.
Ogniotrwałość pod obciążeniem to także temperatura początku mięknięcia, ale w wyniku pewnego określonego nacisku. Temperatura, w której wyrób może pracować, to poziom o 10–20% niższy od tego danej.
Skład chemiczny.
W przypadku glinokrzemianów (szamotów itd.) podawana jest zawsze zawartość tlenku glinu Al2O3. Im więcej, tym lepiej. Wyjątkiem są wyroby krzemionkowe, w których ilość tego związku musi się mieścić w określonych wąskich granicach. Szamot zawiera około 36% Al2O3, grupa tych wyrobów kończy się na zawartości 44%. Wyższą zawartością charakteryzują się wyroby wysokoglinowe.
W tej grupie wyrobów najczęściej podaje się też zawartość żelaza przeliczonego na Fe2O3. Tutaj odwrotnie – im mniej, tym lepiej. Żelazo jest generalnie dodatkiem szkodliwym prawie we wszystkich grupach wyrobów.
W glinokrzemianach skład chemiczny dopełnia tlenek krzemu (SiO2). Nie wymienia się go w składzie, ponieważ jego zawartość w tych wyrobach jest jakby oczywista – podobnie jak zawartość azotu w powietrzu, a jest go przecież w powietrzu najwięcej.
Dla wyrobów zasadowych (najczęściej chodzi o magnezyt) podawana będzie rzecz jasna odpowiednio zawartość MgO i szkodliwych w tym przypadku: wapna, krzemu i, jak poprzednio, żelaza. Tym razem nie ma „oczywistego” tajnego składnika.
Poniżej przykład karty katalogowej z własnościami podstawowych wyrobów magnezytowych (magnezjowych)
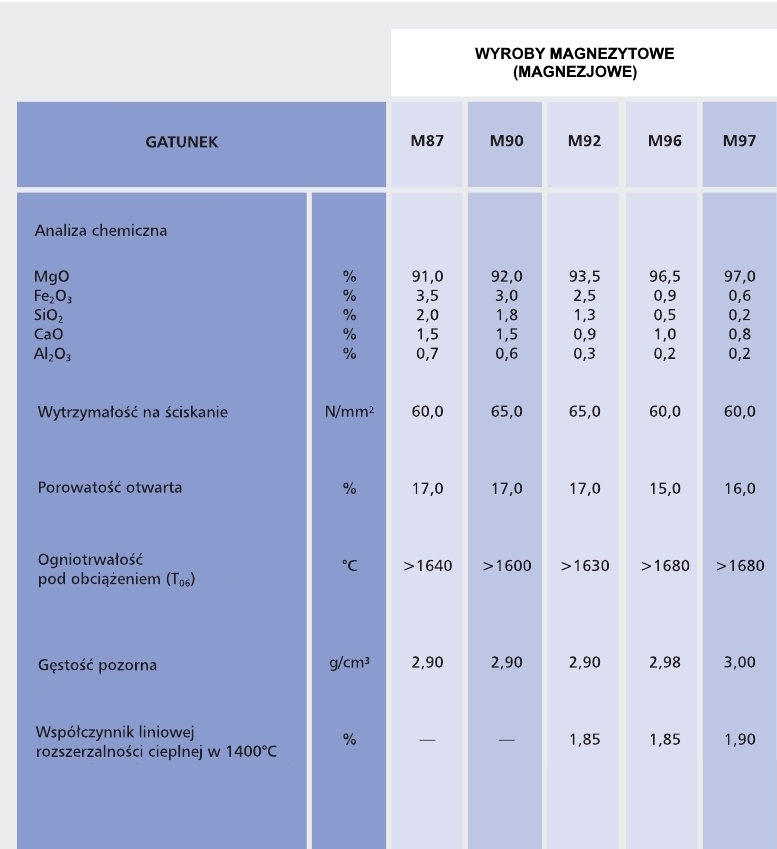
Jak widać, magnezyt to prawie czysty technicznie tlenek magnezu MgO zanieczyszczony głównie tlenkiem żelaza (stąd charakterystyczny brunatny kolor – czysty MgO jest biały).
Na zdjęciu poniżej widać magnezyt o wysokiej czystości uzyskiwany z wody morskiej, używany do wyrobów o najwyższej jakości.
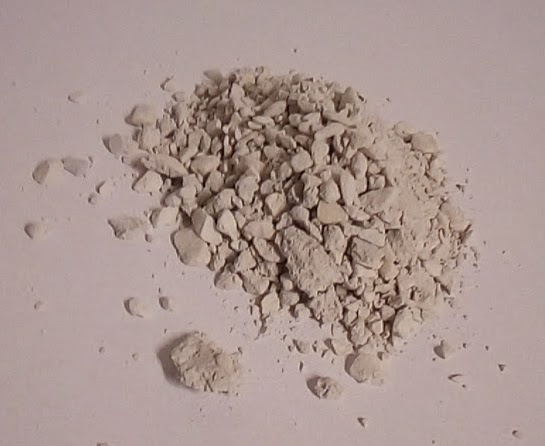
Czasem te „szkodliwe” dodatki dodawane są celowo. Najczęściej jednak nie chodzi o wyroby formowane.
Gęstość.
Większa świadczy o lepszej jakości. Ma bezpośredni związek z wytrzymałością, odpornością chemiczną itd. Generalnie, im wyższy gatunek wyrobu, tym większa gęstość. Jest powiązana ściśle z porowatością – to oczywiste.
Porowatość otwarta.
Im mniejsza tym lepiej, chyba, że chodzi o wyroby izolacyjne. Poziom porowatości to wielkość powierzchni, na którą wyrób przyjmuje destrukcyjne działanie agresywnego środowiska, w którym pracuje. Określa też poziom nasiąkliwości – najczęściej nie chodzi tu o wodę.
Przymiotnik otwarta oznacza, że cegła w takim stopniu może nam czymś nasiąknąć. Jeżeli włożymy ją do wody i odpowietrzymy, to tyle jej „wciągnie”, czyli podstawowa cegła (prostka „1”) o objętości 1,7 dm3 i porowatości otwartej rzędu 20% będzie po tej kąpieli cięższa o 0,34 kg. To bardzo dużo, dlatego zaleca się unikanie moczenia cegieł. Trudno potem te półtorej szklanki wody odparować, a woda pozostawiona w cegle w ogniu może ją po prostu zniszczyć. Może nawet doprowadzić do eksplozji, a nie jest to niestety zjawisko tylko teoretyczne.
Zupełnie niedopuszczalne jest moczenie wyrobów magnezytowych i zasadowych w ogóle. Te dodatkowo jeszcze z wodą reagują.
Wytrzymałość na ściskanie.
Tutaj komentarz nie jest chyba konieczny. Im wyższa, tym lepiej.
Odporność na nagłe zmiany temperatury (wstrząsy cieplne).
Nazwa dość dobrze oddaje cel takich badań. Nie należy się oczywiście przerażać niską liczbą cykli rozgrzewania podawaną w tabelach. Takim szokom temperaturowym na pewno cegła podczas pracy ulegać nie będzie. Rozgrzewa się ją tu do 950 oC, a następnie… wrzuca do wody!. Próby się ponawia, aż do utraty przez cegłę 20% masy (przy każdej próbie od cegły odpadają niewielkie fragmenty).
Przewodność cieplna (więcej) – chyba jasne.
Rozszerzalność cieplna (odwracalna) (patrz: dylatowanie) – chyba też.
Skurczliwość wtórna.
Oprócz „normalnej” odwracalnej rozszerzalności cieplnej (prawie każdy przedmiot, z nielicznymi wyjątkami, rozszerza się po podgrzaniu i wraca do poprzednich wymiarów po schłodzeniu), ceramika wykazuje jednorazowy, najczęściej, skurcz przy podgrzaniu jej do temperatur bliskich maksymalnym. Szczególnie dotyczy to prefabrykatów z betonów ogniotrwałych. Niektóre gatunki, np. wyroby andaluzytowe, wykazują się tu powiększeniem wymiarów.
Dobór.
Kryterium temperatury pracy.
Dobór rodzaju – gatunku – materiału polega na określeniu wobec niego wymagań. Oczywiście podstawowym kryterium jest temperatura, jaką wyroby mogą osiągnąć i pracować przez założony czas. Tutaj, przede wszystkim, trzeba określić zasadność stosowania materiałów ogniotrwałych. Nie zawsze są potrzebne – często zdarza nam się przesadzać. Faktem jest jednak to, że nawet w niższych temperaturach, materiał ogniotrwały daje nam pewność trwałości konstrukcji. Podstawowe materiały konstrukcyjne, nawet ceramiczne, nie są badane pod względem odporności na oddziaływania temperatury wyższej niż temperatura otoczenia lub nieco podwyższonej w związku z naturalnymi sytuacjami mającymi miejsce w życiu. Nie ma potrzeby sprawdzania ich zachowania w kontakcie z ogniem lub spalinami. Nie są też wiele warte amatorskie eksperymenty polegające na wrzucaniu do paleniska kawałka materiału, który chcemy przetestować i wyciąganie z wyniku takiego eksperymentu jakichś miarodajnych wniosków. Nie wiemy co stanie się przy 10. takiej próbie, nie wiemy co stanie się po roku użytkowania, a to, co budujemy, najczęściej jednorazówką ma nie być. Pewność mamy dopiero po odpowiednim dobraniu fachowo przebadanego materiału o, najczęściej, wieloletniej „karierze” w tej dziedzinie.
Jeżeli mamy zamiar zastosować wyrób budowlany w umiarkowanych warunkach pracy, warto zapytać jednak kogoś zajmującego się profesjonalnie dziedziną „trochę” cieplejszych okoliczności.
W miarę bezpieczne stosowanie konstrukcyjnych materiałów budowlanych kończy się w temperaturze 100oC, ceramiki w 300oC. Wyżej, w naturalnych materiałach, które nie były poddawane obróbce cieplnej, mogą zachodzić procesy skutkujące ich zniszczeniem. Mogą one nieraz zachodzić bardzo powoli i być niezauważalne przy nieumiejętnych testach.
Powyżej tej temperatury można stosować standardowe wyroby szamotowe, szamotowe betony ogniotrwałe i żaroodporne. Podobnie jest w przypadku doboru zapraw. Do wspomnianej granicy – zwykłe, powyżej – szamotowe z dodatkami wiążącymi na zimno. Przy zaprawach cementowych wiążących hydraulicznie musimy pamiętać o odczekaniu z rozgrzewaniem czasu koniecznego do związania cementu. Zaprawy oparte na szkłach wodnych i innych środkach wiążących chemicznie, najczęściej wymagają tylko wysuszenia – tu możliwe jest skrócenie czasu oczekiwania.
W tym zakresie temperatur nie ma większego znaczenia gatunek szamotu – możemy się kierować ceną.
Powyżej 600oC sytuacja, może jeszcze nie bardzo, ale już zaczyna się trochę komplikować. Gdy medium mającym kontakt z materiałem jest powietrze, inne nieagresywne gazy czy nawet płomienie, nadal stosujemy wyroby szamotowe (wypalane, betony, zaprawy wiążące na zimno). Problemy mogą jednak już powodować oddziaływania o zasadowym czy alkalicznym charakterze chemicznym, żużle (z węgla kamiennego np.), agresywne gazy np. chlor (ze spalania słomy) czy SO2 (z węgla kamiennego), roztopione reaktywne metale. W przypadku tych oddziaływań musimy stosować już wyroby o podwyższonej zawartości Al2O3 lub wręcz wysokoglinowe, mimo, że, wydawałoby się, jesteśmy jeszcze dużo poniżej granicznych temperatur stosowania szamotu. W umiarkowanych temperaturach i przy ryzyku wykropleń kwasów oraz przy występowaniu spalin z możliwością wydzielania sadzy (atmosfera redukcyjna), stosujemy wyroby ogniotrwałe kwasoodporne (kanały dymowe). Mają one niższą porowatość, a więc zmniejszoną powierzchnię narażoną na chemiczne oddziaływania, oraz obniżoną zawartość żelaza, które katalizuje jedną z reakcji powstawania sadzy. Oczywiście cechy kwasoodporności posiadają też wyroby wysokoglinowe – są to wśród glinokrzemianów produkty najbardziej uniwersalne. Niestety są dość drogie. Gdyby nie to, produkcja szamotów nie miałaby sensu. Kwasoodporność jest zatem równoznaczna ze szczelnością, stosuje się tu więc najczęściej zaprawy zarabiane szkłem wodnym. Nie są to najczęściej wyłożenia pracujące w najwyższych temperaturach.
Graniczną temperaturą stosowania wyrobów szamotowych, praktycznie wszystkich, jest poziom 1350oC. Różnice pomiędzy poszczególnymi gatunkami będą polegały na trwałości.
Podobnie będzie z betonami ogniotrwałymi. Każdy z gatunków może mieć swój odpowiednik wśród wyrobów wypalanych i może być zamiennie stosowany. Przed zastąpieniem trzeba jednak pamiętać o tym, że beton będzie najczęściej droższy od wypalanego odpowiednika, będzie miał niższą przewodność cieplną, będzie bardziej wrażliwy na wstrząsy cieplne. Wyroby wypalane w nietypowych formatach, szczególnie dużych, skomplikowanych i niewielkich lub jednostkowych ilościach, mogą być trudne do pozyskania – betony w takich przypadkach są niezastąpione.
Powyżej tej granicznej temperatury (1350oC) stosuje się już bezwzględnie wyroby o podwyższonej zawartości Al2O3 i wysokoglinowe.
Powyżej temperatury 1600oC zastosowanie mają wyroby z grupy wysokoogniotrwałych. Należą do nich niektóre gatunki glinokrzemianów oraz wyroby zasadowe. Stosowanie tych ostatnich ograniczone jest ich charakterem chemicznym – całkowitym brakiem odporności na oddziaływania kwaśne i wrażliwością na wilgoć. Z tego powodu te akurat wyroby najlepiej sprawują się w wysokich temperaturach. O ile należące do tej grupy wyroby magnezytowe są dość uniwersalne, to innych – dolomitowych – po nagrzaniu schładzać się właściwie nie powinno. Są to wyroby praktycznie wyłącznie znajdujące miejsce w urządzeniach przemysłowych. W domowych realizacjach można wykorzystać ich wysoką gęstość i przewodność cieplną w budowie akumulatorów cieplnych. Powszechnie są zresztą używane do wytwarzania rdzeni elektrycznych pieców akumulacyjnych. Należy też wspomnieć o dużo większej rozszerzalności cieplnej tego typu cegły.
Wysokoogniotrwałe są także wyroby krzemionkowe. Niestety ich nietypowe zachowanie, charakteryzujące się bardzo wysoką rozszerzalnością cieplną w pewnych zakresach temperatur, ogranicza ich zastosowanie głównie do dwóch dziedzin: koksownictwa i hutnictwa szkła. Jako trudne, dla laika, do odróżnienia od wyrobów szamotowych, mogą czasem pojawić się w „drugim” obiegu jako szamot. Ich użycie w urządzeniu pracującym okresowo może doprowadzić do jego zniszczenia. W tej grupie należy jeszcze wymienić wyjątkowo odporne wyroby z węglika krzemu i grupę wyrobów węglowych.
Kryterium oddziaływań chemicznych.
Częściowo już o tej kwestii wspomniano w akapicie wyżej. Okazuje się, że jest niezwykle ważna. Ogromna większość zużycia materiałów ogniotrwałych to zużycie na drodze korozji chemicznej. Wyroby zniszczone przez wysoką temperaturę widuje się bardzo rzadko. Oczywiście obie sprawy się łączą – odporność wyrobów wraz z temperaturę najczęściej spada.
Generalnie, jeżeli chodzi o charakter chemiczny, materiały ogniotrwałe dzielimy na kwaśne, zasadowe i obojętne. Środowisko, w którym pracują, musi być zgodne chemicznie lub temperatura stosowania musi być niższa niż temperatura reakcji. Wszelkie produkty spalania paliw stałych i ciekłych są na ogół kwaśne. Wymusza to stosowanie tam wyrobów kwaśnych lub obojętnych, jakimi są glinokrzemiany. Tutaj więc pozostaje kryterium temperaturowe. Materiały zasadowe stosuje się najczęściej w piecach ceramicznych do wypału surowców budowlanych (wapna, cementu), w piecach metalurgicznych, gdzie stosuje się zasadowe żużle, w regeneratorach lub w urządzeniach wysokotemperaturowych przy braku oddziaływań. Wyroby zasadowe często są znacząco tańsze od odpowiadających im klasą temperaturową glinokrzemianów.
Wśród samych kwaśnych szamotów mamy dość dużo gatunków, nie różniących się na pozór od siebie za bardzo, jeżeli popatrzymy na tabele własności. Wyższy gatunek oznacza jednak większą odporność chemiczną poprzez większą zwartość, gęstość i wyższy reżim technologiczny dotyczący surowców i technologii produkcji. Niestety istotny jest także producent. Akurat jednak dla podstawowych gatunków obowiązuje norma – ale, jak to z normami bywa – nie ma obowiązku stosowania się do niej, jeżeli się na nią nie powołuje.
W przewodach dymowych – kominach – stosuje się specjalnie dedykowane w tym celu wyroby kwasoodporne. Wspomniano już o nich wyżej. Warto dodać, że jest to po prostu impregnowany szamot. Zwykłe wyroby szamotowe nie powinny być stosowane w kominach ze względu na swoją dużą porowatość.
Nie znalazłeś w tekście interesującej Cię informacji? Kliknij poniższy link.